Defoamers: Essential Tools for Enhancing Efficiency in Cleaning Products
Defoamers: Essential Tools for Enhancing Efficiency in Cleaning Products
Blog Article
Exactly How Defoamers Improve Efficiency in Manufacturing and Production

Comprehending Defoamers
Defoamers play an important role in numerous manufacturing processes by properly combating the formation of foam, which can interrupt procedures and influence item quality. Foam can develop in numerous contexts, such as during mixing, home heating, or chemical reactions, potentially causing inadequacies and disparities in items. The device through which defoamers operate normally entails reducing the surface stress of the fluid, enabling bubbles to climb and integrate to the surface area quicker, where they can after that break.
Effective defoamers not just reduce foam development however additionally keep compatibility with the product, making sure that there are no unfavorable effects on the last output. Recognizing the homes and functions of defoamers is necessary for producers aiming to maximize their processes, boost efficiency, and keep the stability of their items (defoamers).
Secret Advantages of Defoamers
Utilizing defoamers in making procedures offers an array of significant advantages that enhance operational performance and product quality. Among the primary advantages is the decrease of foam formation during manufacturing, which can obstruct equipment and interrupt operations. By reducing foam, defoamers make sure smoother procedures, resulting in lowered downtime and maintenance prices.
Additionally, defoamers enhance item uniformity by avoiding air entrapment, which can jeopardize the honesty of the last item. This is particularly crucial in sectors where visual appearance and structure are essential, such as in paints, layers, and food. Improved item top quality not just meets customer expectations but likewise enhances brand name online reputation.
Furthermore, defoamers can help in enhancing source usage. By enhancing the performance of basic material application, they add to cost savings and reduced waste, straightening with sustainability goals. The application of defoamers can lead to much shorter handling times, making it possible for manufacturers to increase production ability without substantial resources financial investment.
Applications in Numerous Industries
In manufacturing processes throughout numerous sectors, the application of defoamers plays a vital function in improving effectiveness and item quality. These chemical ingredients are employed in fields such as food and drink, drugs, and textiles to reduce foam-related challenges.
In the food and beverage sector, defoamers are essential during the fermentation process, preventing foaming that can interfere with production and spoil the product's stability. Similarly, in the pharmaceutical sector, defoamers are made use of in the formula of liquid medications, making sure uniformity and security while decreasing waste.
Fabric production likewise profits from defoamers, as they are utilized in dyeing and completing processes to advertise even circulation of dyes and chemicals. This application not just improves the end product's look but additionally reduces the amount of water and additional resources power consumed throughout production.
Additionally, in the paper and pulp sector, defoamers assist maintain process performance by decreasing foam that can prevent equipment performance. Generally, the diverse applications of defoamers throughout these sectors emphasize their importance in enhancing production processes and providing top quality products.
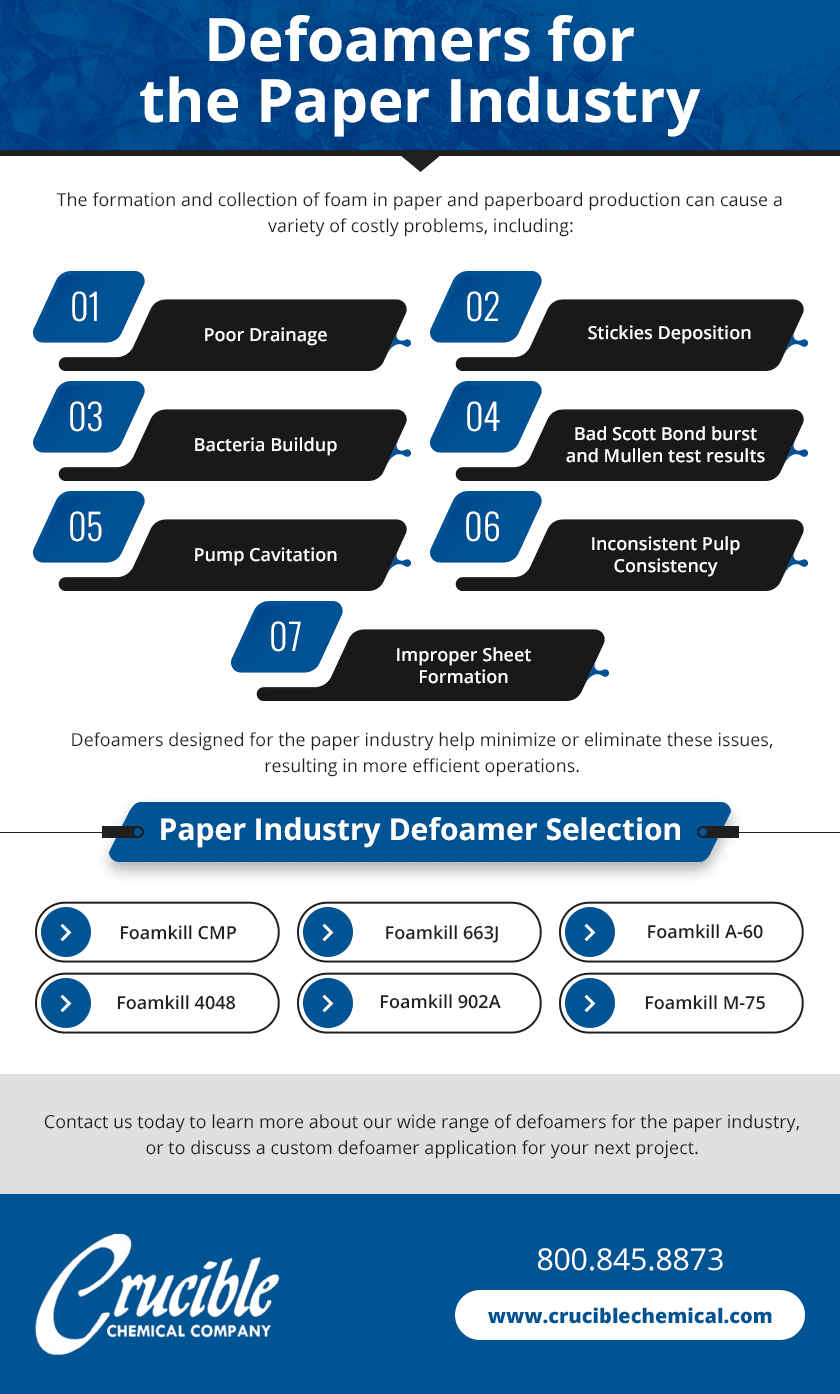
Selecting the Right Defoamer
Picking an ideal defoamer is vital for taking full advantage of performance and top quality in making procedures. The choice of defoamer depends on various factors, including the certain application, the kind of foam being created, and the solution of the item being produced.
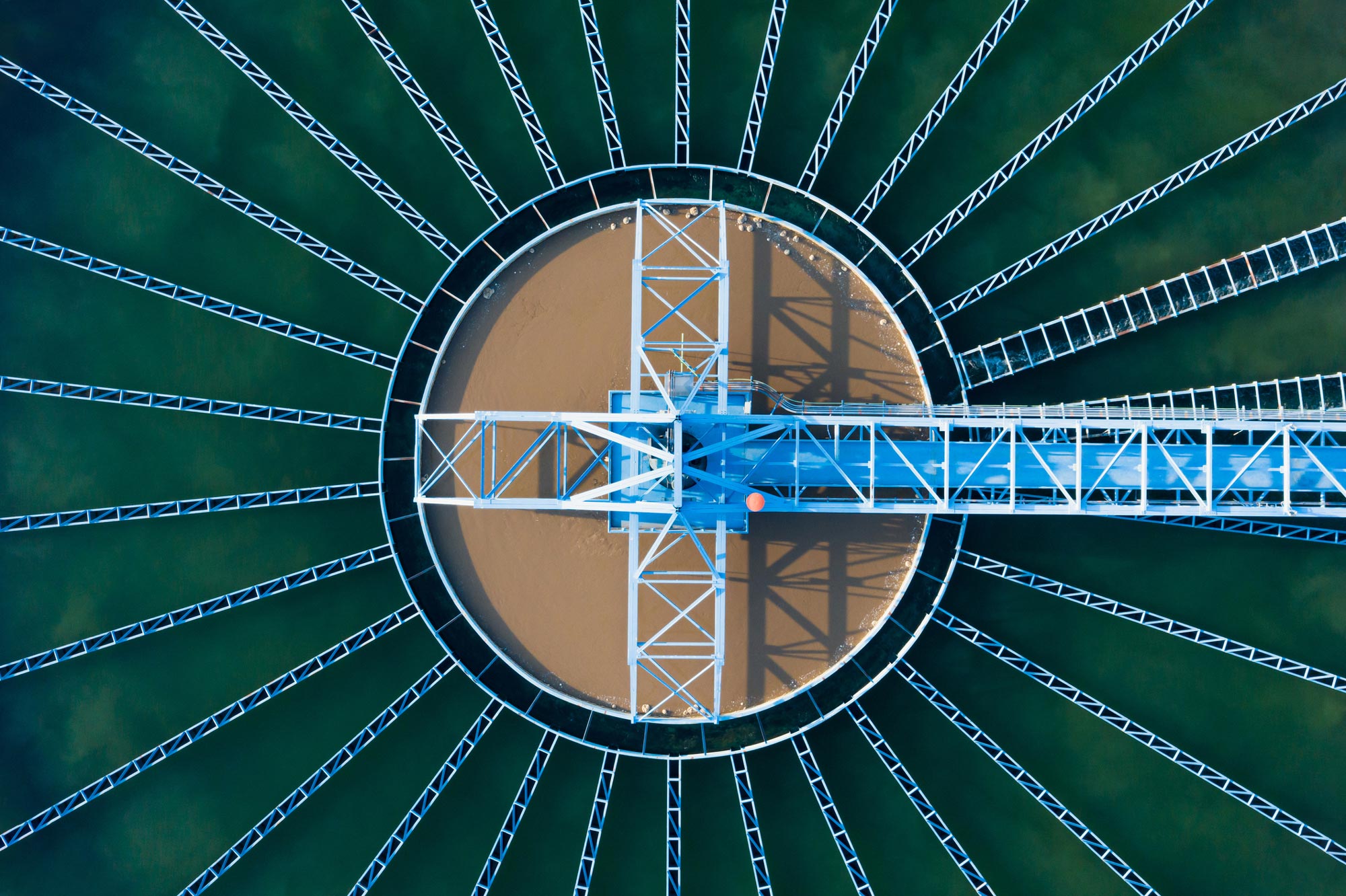
Firstly, consider the chemical compatibility of the defoamer with various other active ingredients in your solution. A defoamer that engages negatively with other parts can negatively affect item top quality. In addition, the temperature level and pH variety during handling are vital; some defoamers do efficiently under certain conditions while ending up being ineffective in others.
Second of all, review the defoamer's performance characteristics, such as its ability to quickly lower foam and its determination during manufacturing. It is necessary to choose an item that not only eliminates foam quickly but additionally maintains its performance in time.
Lastly, think about governing and environmental aspects, particularly if your production procedure goes through rigorous compliance standards. Choosing a low-toxicity find this or naturally degradable defoamer can help satisfy sustainability objectives while guaranteeing functional performance. By thoughtfully assessing these requirements, suppliers can make informed decisions that boost productivity and product stability.
Ideal Practices for Implementation
Effective implementation of defoamers in producing procedures calls for mindful preparation and adherence to ideal techniques. Picking the appropriate defoamer, as formerly discussed, is vital; ensure it is compatible with the materials entailed and addresses the determined frothing concerns efficiently.
Next, keep clear interaction with all stakeholders, including operators and top quality control groups. Educating sessions can help make sure that everybody understands the dosing treatments, potential impacts on product top quality, and safety and security factors to consider. Implementing a test phase can also be advantageous; monitor efficiency closely to evaluate effectiveness and make necessary changes.
Furthermore, regular screening and monitoring of foam degrees can supply like it useful understandings right into the defoamer's performance with time. Changing dosages in action to changes in manufacturing variables will certainly assist maintain ideal efficiency - defoamers. Recording all procedures and results advertises constant renovation, allowing for fine-tuning of defoamer usage and enhancing general performance in producing procedures.
Verdict
In summary, defoamers play an essential function in enhancing effectiveness within production and manufacturing processes. By decreasing foam formation and promoting bubble coalescence, defoamers add to enhanced product quality, consistency, and functional performance. Their application across numerous sectors underscores their adaptability and relevance in optimizing resource use and lowering handling times. Inevitably, the strategic application of defoamers allows suppliers to increase production capability successfully, thereby satisfying client assumptions and attaining price financial savings.
The advantages prolong to product quality and cost savings, as defoamers assist enhance processes.Defoamers play an important function in different manufacturing processes by effectively combating the development of foam, which can influence and interfere with procedures product quality. Understanding the residential properties and functions of defoamers is important for producers aiming to maximize their processes, enhance productivity, and keep the stability of their items.
Using defoamers in producing processes supplies a variety of significant advantages that improve operational performance and product quality.Additionally, defoamers boost item consistency by avoiding air entrapment, which can compromise the integrity of the final item.
Report this page